01. 09. 2020
Verfasst von: Yorck Hedicke-Claus
Automatisierung verkürzt Planungsprozess für Schmiedeteile
Um Schmiedeteile herzustellen, werden Rohformen schrittweise umgeformt. Der Planungsprozess hierfür ist bisher kosten- und zeitintensiv. Die Qualität der Stadienfolge hängt zudem von den Fähigkeiten der Konstrukteure ab. Das Institut für Integrierte Produktion Hannover automatisiert deshalb die Planung und spart dadurch Zeit und Material ein.
Zeit, Material und Energie einsparen
Mittelständische Schmiedeunternehmen müssen aus Wettbewerbsdruck schnell produzieren. Häufig fehlen ihnen die Kapazitäten und erfahrene Konstrukteure, die einzelnen Produktionsschritte eines neuen Bauteils ressourcenschonend zu planen. „Mit dem üblichen Vorgehen dauert dieser Planungsprozess teil-weise Wochen", erklärt Yorck Hedicke-Claus vom Institut für Integrierte Produktion Hannover (IPH). Aus diesem Grund entwickelt das IPH-Team eine Methode, die automatisiert die Stadien von der Rohform bis zum fertigen Bauteil besonders materialeffizient plant. „In Zukunft erfolgt die Stadienplanung in Minuten“, stellt der Projektleiter in Aussicht.
Intuitiver planen, Gratanteil reduzieren
Bisher verwenden Konstrukteure die zeitaufwändige Finite-Elemente-Methode als Planungswerkzeug zur Auslegung der Stadienfolge von der Rohform (Halbzeug) ausgehend zum Schmiedeteil. Das neue Verfahren dreht diesen Prozess um: Es berechnet den Weg rückwärts vom fertigen Bauteil zum Halbzeug und erstellt die einzelnen Stadien des Umformprozesses somit intuitiver. „Bei einer optimalen Planung reduziert sich der Gratanteil“, erläutert Yorck Hedicke-Claus. „So sparen die Betriebe Zeit in der Entwicklung der Stadienfolge sowie Material und Energie in der Produktion."
Ausgangspunkt der neuen Methode ist eine 3D-Skizze des gewünschten Bauteils im CAD-Format, aus der die Forschenden Größe, Kontur und andere geometrische Daten ermitteln. Dieses Modell unterteilen sie dann in verschiedene Ebenen und bestimmen für jede den Flächeninhalt und Schwerpunkt. Unter Beachtung von umformtechnischen Regeln nähern sie diese Werte Schritt für Schritt an die Massenverteilung des Halbzeugs an. So lassen sich Riss- und Faltenbildung verhindern und der Gratanteil als überschüssiges Material verringern.
Alternative bei Fachkräftemangel
Da diese Regeln nun mit dem Computerprogramm mathematisch erfasst sind, ist die Planung künftig unabhängiger vom erfahrenen Fachpersonal. Haben die Forschenden vom IPH die Programmierungsarbeit abgeschlossen, erfolgen umfassende Test- und Anpassungsphasen. Das Forschungsprojekt wird über die Arbeitsgemeinschaft industrieller Forschungseinrichtungen (AiF) und vom Bundeswirtschaftsministerium gefördert.


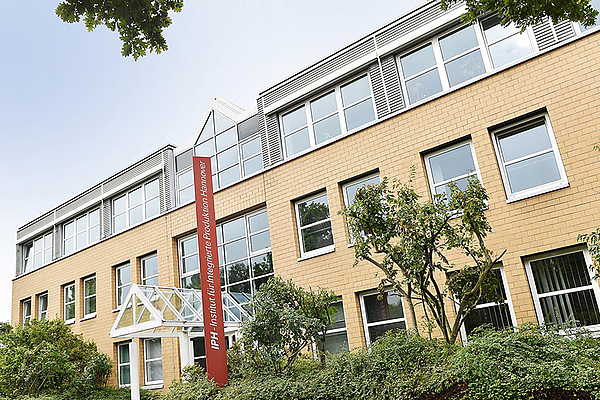
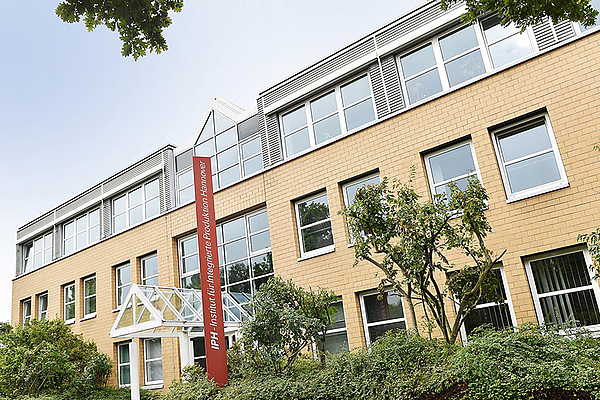
30419 Hannover Germany